Collaboration to advance naval shipyard technology
DMTC Limited is working with BAE Systems Maritime Australia, ANSTO and the University of Wollongong to develop advanced welding technologies for use on naval shipbuilding programs such as the Hunter Class Frigate Program.
Collaboration between the industry, research and academic organisations will take place over two years and is expected to result in production efficiencies in the construction of complex warships by incorporating artificial intelligence to reduce weld rejection rates, increase throughput and improve workforce skills in shipbuilding.
Investment and technology development across the highly automated Osborne Naval Shipyard is driving digital transformation in shipbuilding through advanced robotics, additive manufacturing and Industry 4.0 utilisation and, while Osborne’s production facilities incorporate state-of-the-art robotic welding, the organisations believe this phase of research and development could identify opportunities to further automate and optimise weld sequencing, which is critical in ensuring the stability and life of welded structures such as steel bulkheads and panels.
Weld sequencing for ship construction is considered a complex, manual and time-consuming process and the research will focus on an optimal model that improves structural analysis to reduce “distortion” in the welding of units and the 22 blocks that make up each Hunter frigate.
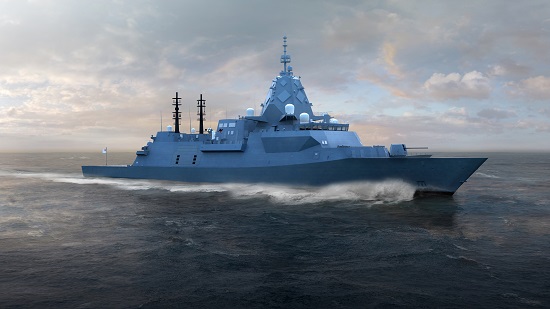
BAE Systems Maritime Australia is designing and building nine of the world’s most advanced anti-submarine warfare frigates for the Royal Australian Navy. Image courtesy of BAE Systems Australia
The project will establish a sovereign capability in optimising weld sequencing and builds on DMTC’s long history in working on industrial projects to reduce weld-induced distortion on various defence platforms.
The research forms part of broader work to deliver Australian Industry Capability outcomes under DMTC’s Naval Shipbuilding and Sustainment Program, an industrial innovation partnership with Defence’s Capability Acquisition and Sustainment Group.
Read the full media release here.
Posted by Harry Baxter on January 27th, 2022 Tagged: collaboration, DMTC, Shipbuilding, technology, Welding